HPAPI Processing and Drying Suite
Purpose: A two-part enclosure consisting of a Single Pass Air Flow Glove Box Enclosure and a Nitrogen Purge Enclosure was designed to provide protection to the operator and product. The left side uses HEPA-filtered supply air as well as HEPA exhaust to create a clean interior environment, while the right side provides a clean, dry nitrogen environment.
Process: The process included wetcake narcotic being oven-dried to a powder to remove water, methanol, ethanol, IPA, DCM, chloroform, acetone, and ethyl ether. After drying in the oven, 9”x13” glass trays were to be moved from the oven to a balance area for weighing. Once the final weight is measured and recorded, the material is moved to the packaging operation.
Equipment: A suite was designed which included flame retardant polypropylene superstructures, a central transfer port, inlet HEPA filtration, dished black phenolic bases, top mount fans with BIBOs and HEPAs, independent hinged doors (24.635 W x 27” H opening), (7x) 10” oval glove ports, 12” H x 16” W access door, FS1650 alarm, minihelic gauge, stainless steel tables, and glass viewing panels. Glass viewing panels and LED lighting to maximize lighting across the workspace. The system had an exterior width of 168”, a depth of 43”, and an interior height of 41”. 245 CFM was required at the thimble connection to maintain 50LFM at center cross section of the isolator, while 216 CFM was measured at the fan to maintain the same LFM at the center cross section. Negative pressure was measured at the mouth of the house exhaust hose at the N2 connection. Multiple glove ports were required due to cleaning requirements, so a design was created to have ports at two different horizontal levels to allow access to the oven controls and oven door in the isolator portion of the enclosure. An N2 generator existed on-site which was hard-piped into the room. Nitrogen is used as an atmospheric replacement during this process. Nitrogen-filled environments can be kept at low relative humidity levels as a consequence of the original purity of the supply. Moisture-sensitive products like nanomaterials and APIs are less susceptible to decomposition in such an environment. Two 0.3 micron cartridge filters were installed on incoming and outgoing N2 to ensure a clean environment.
A custom table for the enclosure was developed as a way of supporting the oven and the enclosure, with adjustable feet beneath the oven that could be used to set height and ensure a proper seal in the wall flange.
Peripheral Equipment: The Binder VDL 115 safety vacuum drying oven for flammable solvents had a max temperature of 100 degrees Celsius, requiring the use of Flametec polypropylene as a material of construction for the Processing and Drying suite. Due to the nature of the materials being manipulated, the oven would typically run within a 50- 60 degree Celsius range. Gasket material was made of high temperature RTV silicone with a maximum temperature rating of 343 degrees Celsius to seal the stainless steel flange to the oven. The Binder VDL 115 oven had two aluminum expansion racks with class 2 independent adjustable temperature safety device with visual alarm— components accessible at the front. The oven needed to able to fully open within the isolator with the door swinging outward from left to right.
Peripheral Equipment Considerations: Completely enclosing the oven created a heat concern, solved by the use of Flametec polypropylene and by installing the oven into the exterior wall and using the custom table for weight support. During on-site installation by FSI personnel, to accommodate an added outer control on the oven, the frame had to be cut by hand on the spot. After installation was completed and validation tests initiated, FSI personnel noted that the interior of the oven was sealed but its exterior shell was not. Particles were coming out of the outside of the oven’s sidewall, which made FSI installers fashion a block-off plate to limit escape of particles during oven processing. The client then revised their internal cleanliness protocol from Class 5 to Class 7 upon this conclusion by FSI personnel.
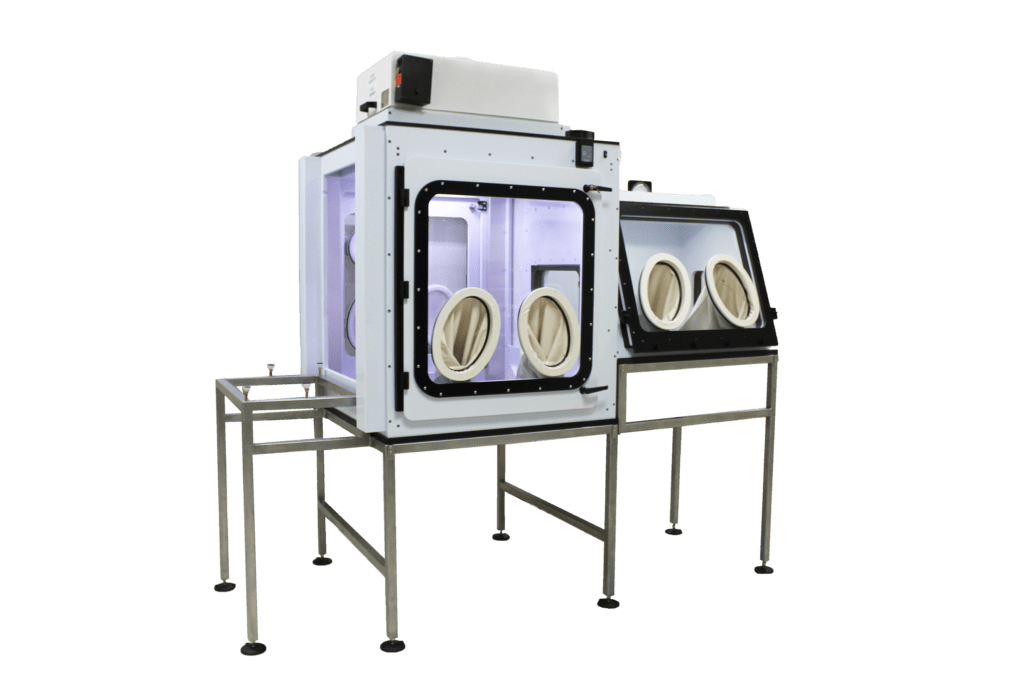
